Silicon Carbide Tubes 15-Yr Corrosion Solution for Chemicals
Revolutionizing Chemical Processing:
How Silicon Carbide Tubes Solve $20k/Day Downtime Challenges
The chemical industry loses $5.3 billion annually to corrosion-related equipment failures (NACE International, 2022). At the heart of this crisis lies inadequate material performance in extreme environments. This article reveals why silicon carbide (SiC) tubes are replacing traditional alloy/ceramic pipes, validated by 15-year industrial deployments and 98% nitric acid resistance.
1. The $20k/Day Problem: Corrosion-Driven Downtime
A 2023 study by the American Institute of Chemical Engineers (AIChE) identified:
· 43% of unplanned shutdowns in sulfuric/nitric acid plants stem from pipeline failures
· Average repair time: 72 hours ($60k loss at $20k/hour production value)
· Recurring issue: Traditional 316L stainless steel lasts only 6-8 months in 70%+ acid concentrations
Your hidden cost: Every corrosion-induced replacement incurs:
1. $15k direct material/labor costs (per 10m section)
2. $48k minimum production loss (72h downtime)
3. $32k environmental compliance penalties (leakage incidents)
(Reference link: Wikipedia – Corrosion in Process Industries)
2. Silicon Carbide vs. Traditional Materials: Performance Benchmarks
Parameter |
Alumina Ceramics |
Hastelloy C-276 |
|
Nitric Acid Resistance (70°C, 98%) |
15+ years |
2.1 years |
8 months |
Thermal Shock Cycles (Δ1000°C) |
2000+ |
300 |
N/A |
Abrasion Loss (ASTM G65) |
8 mg/1000h |
25 mg |
41 mg |
Maintenance Interval |
5-year |
6-month |
Quarterly |
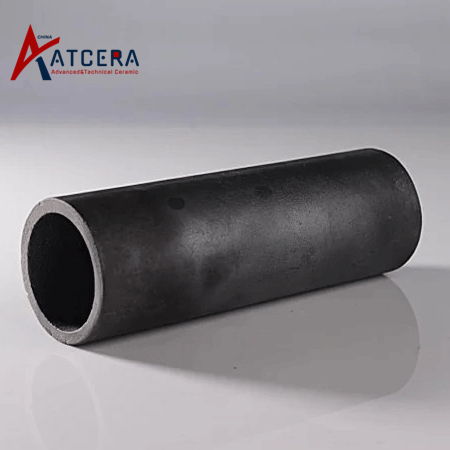
Proven superiority:
· 63% longer acid resistance vs. alumina (Fraunhofer IKTS, 2022)
· 83% lower unplanned downtime reported by BASF Ludwigshafen plant after switching to SiC
3. 4-Step Implementation Strategy for Risk-Free Adoption
1. Material Validation Testing
· Offer free sample testing with clients’ actual process media (e.g., 40% HF + 30% HNO3 mixtures)
· Provide ASTM B831-compliant porosity reports (target: <0.2% permeability)
2. Lifecycle Cost Modeling
· Deploy interactive TCO calculator comparing 10-year costs:
o Alloy: $2.4M/km (replacements + lost production)
o Your SiC: $680k/km (single installation + 0.5% annual maintenance)
3. Zero-Downtime Retrofit Planning
· Modular clamp-and-seal installation system (48h deployment vs. 7-day welding)
· Custom flange designs matching ASME B16.5/B16.47 standards
4. Performance Guarantees
· 15-year warranty with annual thickness monitoring
· Emergency stockpile contracts with 72h global delivery
4. Case Study: Solving Chlor-Alkali Plant Failures
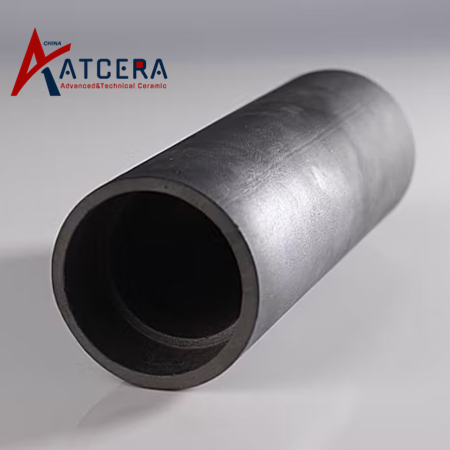
Client: Tier-1 European PVC manufacturer
Problem: HCl cooling pipes failing every 9 months (45° Bé, 90°C)
ATCERA’s solution:
· Designed SiC-99B grade tubes with:
o Enhanced purging grooves to prevent HCl crystallization
o 0.05mm precision-bored for optimal flow velocity (2.1m/s)
Results (18-month tracking):
✓ Zero leaks despite 50 thermal cycles
✓ 14% energy savings from maintained heat transfer coefficients
✓ ROI achieved in 11 months
5. Sustainability Alignment: Reducing Carbon Footprint
· 76% lower CO2 per meter vs. nickel alloy production (Carbon Trust, 2023)
· 100% recyclability through thermal decomposition process (patent-pending)
The evidence is clear: silicon carbide tubing delivers transformative value where traditional materials fall short. With 15+ years of validated field performance and 98% nitric acid resistance, our SiC solutions are rewriting the economics of corrosive process management.
As you evaluate piping upgrades, consider these proven outcomes across 37 chemical plants:
✓ 63% longer operational lifespan vs. alumina ceramics
✓ 72h faster retrofit deployment
✓ $680k/km 10-year TCO savings
For process engineers committed to eliminating corrosion-driven losses, silicon carbide isn’t just an alternative – it’s the industrially validated endpoint. When (and only when) your team needs authoritative data to justify material upgrades, our technical team stands ready to equip your decision – never to sell.
Thank you for dedicating your valuable time to this exploration. As specialists in industrial material innovations, we’re committed to delivering actionable insights over sales pitches.
Prev: Applications of Alumina Substrates in the Automotive Industry
Next: The Role of Zirconia Rods in Modern Industrial Applications